









| |
Vision Sensors
"Smart" Inspection
Cameras
Why Vision
Sensors?
Repetitive inspection of production lines is a labour-intensive
activity that is being replaced by vision sensors which are not only
cost-effective, but give consistency of judgement and documented
traceability to the inspection process.
How do they
work?
Vision sensors have huge numbers of photoelectric cells that capture
a complete image. The amount of detail (the resolution), expressed
as the pixel count depends on how many photoelectric cells the
sensor contains (e.g. 1.3 million pixels). After capturing the image, the
vision sensor compares some, or a number of characteristics of the image to the reference image stored in its memory.
So, if the sensor is set to recognize a blister pack with eight undamaged
tablets, it knows to reject a pack that has only seven tables or a broken
tablet. Also the packet can be anywhere within the camera’s field of view. And
it can inspect asymmetrical objects no matter how they are rotated within a full
360o range. They have a wide variety of production applications.
Which characteristics the sensor compares to the reference image is
set using software
inspection
tools built into the sensor. Some sensors have all the
available software tools built-in and some simpler sensors have only
the tool they need to do a particular task, saving cost and
simplifying both set-up and operation. |
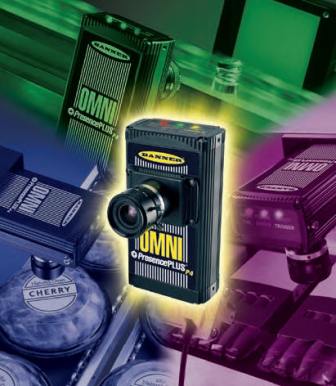 |
The sequence
begins when sensor is triggered to take an image. The sensor has
been programmed to enable it locate, analyse and measure the image
and then compare the results with preset pass or fail criteria. The
result is communicated over Ethernet or RS232 coms ports. The
Tools
which enable the sensor locate, analyse, measure and decide are
important features for the effectiveness and simplicity of the
system. For many applications, a simple "Teach" facility is a huge
benefit. |
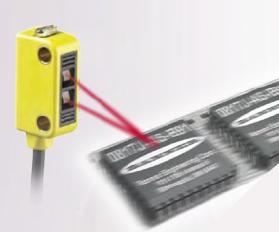
Trigger Sensor |
Vision Sensors
can often be selected more easily from known applications where the
various parts have been specified.
See Below.
Please
contact us if you wish to ask for further advice or a
product demonstration.
You may prefer to see the full
Sensor Range
The following application examples are
provided to assist in seeing the potential for vision sensors in any
manufacturing environment.
|
APPLICATIONS: |
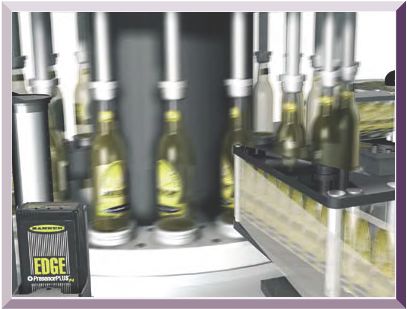
Label Alignment
Objective: To
verify that the labels on a bottle are aligned with each other and
both are straight.
Sensors: Presence PLUS P4 EDGE, with
LCF08 lens,
HFFW12DC
tubular fluorescent light, PLC used as a trigger.
Operation: Two labels are glued to the front of a bottle –
one on the neck and another on the body. The
Presence PLUS P4
EDGE’s
Locate tool finds the edge of the bottle, and then the two Edge
tools verify that the top and bottom labels are lined up and not
skewed. |
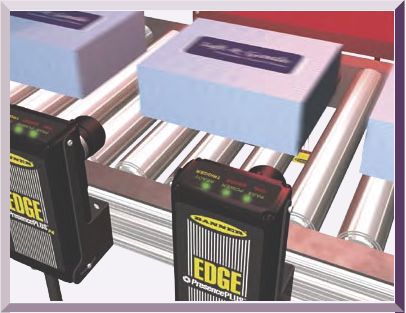
Complete Assembly Inspection
Objective: To
verify that each end flap on a cardboard carton is glued down.
Sensors: Presence PLUS P4 EDGE, with
LCF08 lens, LEDRB85X220M
red backlight, fixed-field photoelectric used as a trigger.
Operation: After a cardboard carton is packed, the flaps on
both ends are glued down. The
Presence PLUS P4
EDGE’s Locate tool
finds the edge of the box, then the Edge tools checks whether the
upper and lower horizontal edges are the same distance from the
centre of the box. If not, the flap is not glued, and the box fails
the inspection. |
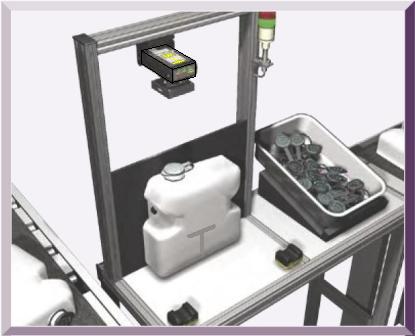
Part Presence/Absence & Orientation
Objective: To
verify that the cap of a washer reservoir is present and oriented
within an accepted range of rotation.
Sensors: Presence PLUS P4 GEO with
LCF16 lens,
LEDRR62X62 red
ring light, Verification Touch Button (VTB) used as a trigger.
Operation: An operator places a capped reservoir on the
inspection stand. The Presence PLUS P4 GEO’s Geometric Count tool
verifies that the cap is on the reservoir, that the logo is printed
on the label, and that the cap is not rotated beyond the accepted
range. |
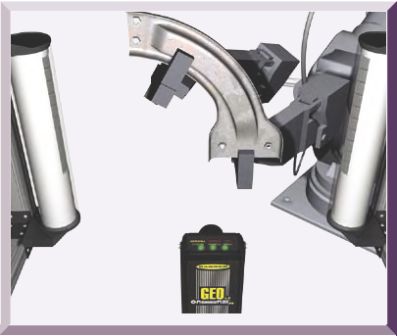
Component Inspection
Objective: To
verify that all weld nuts in an automobile door component are
present, oriented with the right side up and in the correct
location.
Sensors: Presence PLUS P4 GEO 1.3 with
LCF16LMP lens,
HFFW24AC tubular fluorescent light, PLC used as a trigger.
Operation: Nuts are welded to a component of an automobile
car door. The Presence PLUS P4 GEO uses four Geometric Count tools
check whether the weld nuts are correctly oriented and aligned over
the bolt holes. |
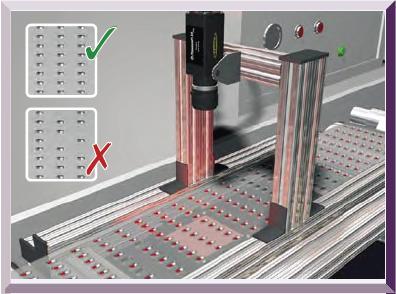
Blister Package Verification
Objective:
To verify that the blister packet is
filled with a complete tablet of medication in each cell and that
the blister is free of debris.
Sensors:
Presence
PLUS
Pro vision sensor,
LEDRB85X220W red diffused backlight, PLC used as a trigger.
Operation:
A blister machine fills each cell on
a web of blister packets with a tablet. Before the packets are
sealed and cut, the
Presence
PLUS
Pro uses the Blob
tool function to inspect each row to verify each cell has a complete
tablet inside and also ensures no broken tablets or other debris are
incorrectly packaged. If a missing or partial tablet is found, the
blister is rejected. |
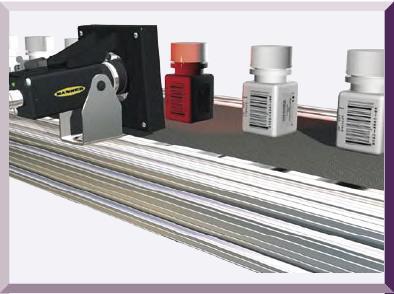
Label Positioning
Objective:
To verify correct label placement on
bottles of tablets.
Sensors:
Presence
PLUS
Pro vision sensor, with
LCF16 lens,
LEDRR80X80W red ring light, photoelectric sensor used as
a trigger.
Operation:
As bottles of
tablets pass on a conveyor, the
Presence
PLUS
Pro
verifies that the label is present and positioned correctly. The
Edge and Measure tools measure the distance between the top of the
label and the top of the bottle to check height. The distance
between the side of the label and the side of the bottle is also
measured to make sure the label is centred on the face of the
bottle. |
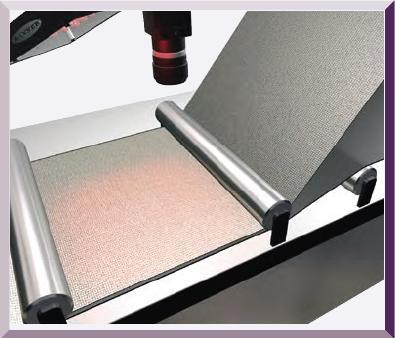
Assembly Verification
Objective:
To verify that cloth belting has been
added to a band of tyre rubber
Sensors:
Presence
PLUS
Pro vision sensor, with
LCF25R lens,
LEDRA80X80W red area light, PLC used as a trigger.
Operation:
On a web, cloth belting is bonded to
one side of a band of hot rubber. Using the Average Grey Scale tool,
the
Presence
PLUS
Pro detects the difference between
the brightness of the cloth and the darkness of the rubber to make
sure the cloth has been applied to the rubber. |
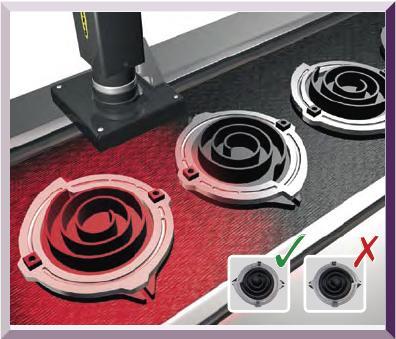
Part Orientation Verification
Objective:
To verify that a ring is placed correctly on a component of an
assembled part.
Sensors:
Presence
PLUS
Pro
vision sensor, with LCF08 lens,
LEDRR80X80W red ring light, PLC used
as a trigger.
Operation:
An assembler places the ring over the part. The ring fits in two
possible positions, but only one position is correct. The
Presence
PLUS
Pro
uses the Edge tool to check that the gasket is in the correct
position, within an accepted variation of rotation. |
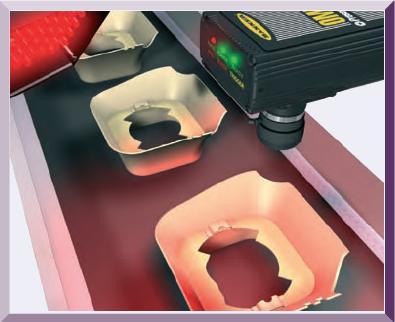
Component Moulding Inspection
Objective:
To inspect moulded plastic steering
wheel components for excess or deficient material.
Sensors:
Presence
PLUS P4 OMNI 1.3, with
LCF08LT
lens and LEDRA80X80M red area light.
Operation:
After a steering wheel component is
removed from the mould, the
P4 OMNI 1.3 inspects it for areas
that received too much or too little material during the moulding
process. Defective components are diverted from the line. |
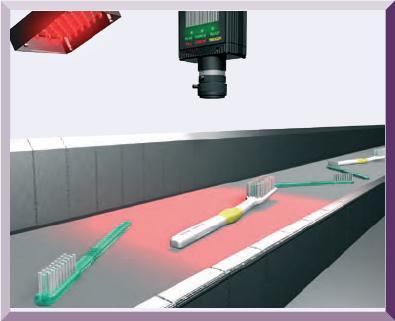
Toothbrush Sorting
Objective:
To sort different styles of
toothbrushes before they are packaged.
Sensors:
Presence
PLUS P4 OMNI, with
LCF08LT
lens and LEDRA80X80M red area light.
Operation:
As toothbrushes pass on a conveyor,
the P4
OMNI detects shape differences, regardless of their
orientation on the conveyor. The different styles are automatically
separated at the end of the line, before they are packaged.
|
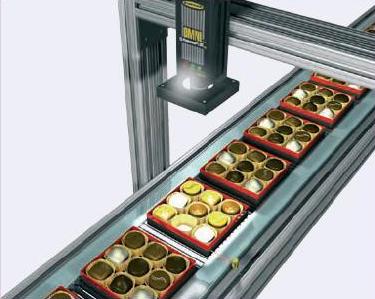
Food Packing Inspection
Objective:
To inspect
boxes of chocolates for missing or damaged pieces to make sure each
nest contains a candy and that the candies are not damaged.
Sensors:
Presence
PLUS P4 OMNI with
LEDR80x80M light and
LCF16LMP lens.
Operation:
After boxes of
chocolates are filled, the
P4
OMNI checks
whether the box contains the correct number of pieces. It also
checks that the shapes of the candies are within tolerance, to
verify that none are damaged.
|
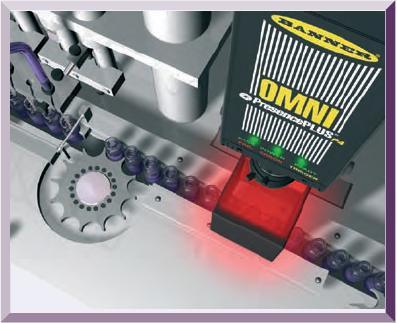
Glass Vial Integrity Check
Objective:
To check for damaged lips on glass
vials on a high-speed filling line.
Sensors:
Presence
PLUS P4 OMNI with LEDRO50N
light and LCF50LMP lens.
Operation:
Glass vials can be damaged during filling
and transfer. The P4
OMNI inspects the opening, or lip, of
each vial as it passes on a high-speed conveyor to detect vials with
chipped or cracked lips. If it detects any damage, it diverts the
vial from the line before it is sealed and capped. |
|