Ultrasonic sensors are
designed for contactless and wear-free detection of a variety of
targets by means of sonic waves. It is not important whether the
target is transparent or coloured, metallic or non-metallic, firm,
liquid or powdery. Environmental conditions such as spray, dust or
rain seldom affect their function.
Sensing modes
Ultrasonic sensors are mainly used in the diffuse mode. An object in
front of the sensor is detected by its reflection of a part of the
emitted sound wave. It is also possible to use ultrasonic sensors in
the opposed and reflective mode. An ultrasonic opposed mode sensor
consists of an emitter and a receiver which “listen” to each other
permanently. The ultrasonic sound is interrupted by an object
between the emitter and receiver and the sensor generates a
switching signal.
Beam Angles: M18/M30
(threaded metal barrel) and Q30 sensors (rectangular plastic
housing) have a very narrow sonic angle of approx. 6° and are
especially suited for precise detection of relatively small targets.
The concentration of the sonic beam provides sensing ranges of up to
8 m. The sonic cones of our Q45U and T30U sensors are between 12 and
15°. The sensor type CP40 (rectangular plastic housing) has a much
wider sonic cone (60°). These devices are suited to monitor a large
area and to detect smooth, flat and even tilted objects.
Adjustments With
almost all ultrasonic sensors it is possible to adjust the lower and
the upper limit of the switching or measuring range. Objects outside
this range may be detected, but they don’t initiate the output to
change state. Q45U sensors are equipped with DIP switches for
adjustment of several parameters such as the sensor’s response time,
it’s performance during a loss of the echo, or in case of direct
operation of a pump in conjunction with the sensor.
Repeat accuracy
Among other factors such as the wave length, the accuracy of
ultrasonic sensors is mainly limited by speed fluctuations of the
sound during temperature changes. Therefore some of the sensors
feature temperature compensation. This enables analogue Q45U sensors
to achieve a repeat accuracy of up to 0.6 mm over a wide temperature
range.
Output functions:
Ultrasonic sensors with switching output are available in all
housing types. M30, T30U and T50U type sensors also come with two
switching outputs (e.g. for minimum and maximum level control).
Versions with an analogue current or voltage output are included in
most housing styles.
Noise suppression: Noise
such as metal "clink" or pressure "hammering" do not influence the
evaluation due to optimised selection possibilities of the frequency
range and the patented noise suppression circuitry.
Synchronisation: In
most cases, sensor synchronisation will prevent mutual
interferences. Most sensors of the series RUC...M30, RU...M18 and
RU...Q30 are capable of self-synchronisation by simply connecting
the synchronisation line. Synchronised sensors emit sonic pulses
simultaneously. When mounted correctly, they perform like a single
sensor with an extended detection angle.
|
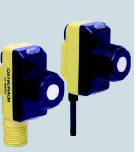
QS18U
Range:
500mm
Output: Switch (pnp or npn)
Mode: Diffuse or Retroflective
Adjustment: Teach |
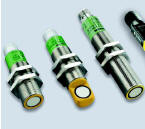
M18/S18U
Range: 1 m
Output: Switch (pnp) or Analogue (4-20mA)
Mode: Diffuse or Retroflective
Adjustment: Pot or Program or Teach |
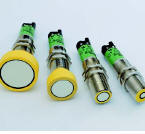
M30
Range: 6 m
Output: Switch (pnp or 2x pnp) or Analogue (4-20mA)
Mode: Diffuse
Adjustment: Pot or Program |
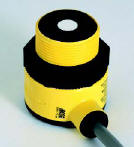
T30U
Range: 2 m
Output: Switch (pnp or npn) Analogue (4-20ma/0-10V)
Mode: Diffuse
Adjustment: Teach |
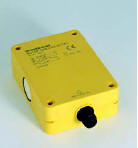
Q30
Range:
1 m
Output: Switch (pnp) or Analogue (0-10V)
Mode: Diffuse
Adjustment: Pot |
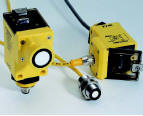
Q45U/UR
Range: U = 3
m, UR = 250 mm
Output: Switch (pnp or npn) or Analogue (4-20mA/0-10V)
Mode: Diffuse
Adjustment: Teach |
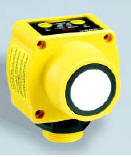
QT50U
Range:
8 m
Output: Switch (pnp or npn) or Analogue (4-20mA/0-10V)
Mode: Diffuse
Adjustment: Teach |
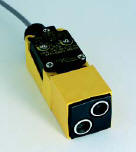
CP40
Range:
1.8 m
Output: Switch (pnp) or Analogue (4-20mA/0-10V)
Mode: Diffuse
Adjustment: Pot |
Sensing conditions
The ultrasonic transducers are especially optimised for the medium
"air". The sensors can also be used for other gaseous media but then
they require a sensitivity adjustment.
Blind zone
Diffuse mode ultrasonic sensors are not capable of detecting targets
which are located directly in front of the sonic transducer. The
area between the sonic transducer surface and the beginning of the
detection range is called blind zone and must always be kept free.
Air temperature and humidity
Both air temperature and air humidity influence the sonic pulse
duration. An air temperature increase of 20 °C leads to a change of
the sensing distance of up to +3.5 % when using the M30 or the Q30
version (resp. +8 % with the CP40-sensor), whereas the distance of
the object seems to decrease. An increase of humidity results in an
increase of the sound speed of max. 2 % as opposed to dry air
conditions.
Air pressure
Normal atmospheric changes of ± 5 % (for a local reference point)
can lead to a deviation of the sensing range of about ± 0.6 %.
Air streams
Air streams influence the echo time, however, air flow speeds of up
to 10 m/s are insignificant. In conditions where turbulences
prevail, e.g. above glowing metal, the use of ultrasonic sensors is
not recommended, because the echo of distorted sound waves is
difficult to evaluate.
Environmental conditions
Normal concentrations of rain or snow do not affect the sensor but
direct wetting of the transducers should be avoided. The transducer
types CP40 are not protected against humidity (degree of protection
IP40). All other ultrasonic sensors are not damaged by water but
correct functionality may be impaired. Therefore, the ultrasonic
transducers should generally not be subjected to direct wetting.
Targets
Solid, fluid, granular and powdery targets can be detected by the
ultrasonic sensor. The surface variation of the object should not
exceed 0.15 mm. Larger variations may lead to a reduction of the
sensing range. However, such targets do not require exact alignment.
The target colour has no influence on the sensing distance, also
transparent targets like glass or clean plastic are reliably
detected. The temperature of the target influences the sensing
range: hot surfaces reflect the sonic beam wave less than cold ones.
The ultrasonic reflectivity of liquid surfaces is the same as that
of solid, flat objects. Correct alignment should observed. Textiles,
foams, wool, etc. absorb the sonic wave. The sensing range will be
reduced. Simultaneous operation of multiple sensors When multiple
ultrasonic sensors are used, mutual interference of the sound cones
may arise. Here, either sensor synchronisation, alternate sensor
operation, or a minimum distance between the sensors will solve this
problem.
Synchronisation
Synchronisation of ultrasonic sensors causes the sensors to emit the
sonic pulse simultaneously. Using the series RUC…- M30, RU…-Q30 und
RU…-M18 enables synchronisation of sensors by connecting the
X1-line. Selecting the synchronisation mode to avoid mutual
interferences is only recommended for applications where the sensors
are mounted closely to each other and emit in approx. the same
direction. In this mode, the sensors perform like a single sensor
with an extended sonic cone. When a synchronised sensor switches,
the target may be in front of the switching sensor as well as in
front of one of the other sensors. Typical applications are level
control monitoring with more than two switching points or
large-scale ramp control tasks.
Alternate sensor operation (multiplexing)
Ultrasonic sensors, which operate alternately, are fully independent
from each other and mutual influencing is impossible. The more
sensors are operated alternately, the lower the switching frequency.
The X1-line of the sensor series RUC…- M30, RU…-Q30 and RU…-M18 can
also be used as an enable input for multiplex purposes. If the
X1-line is connected to +24 V, the sensor is enabled; if the X1-line
is connected to 0 V, the sensor is disabled. Multiplexing via the
X1-line has the advantage that for each enable-operation only the
response time and not also the time-delay before availability has to
be considered.
When using the programming device RU-PDI most sensors can be
programmed automatically for multiplex operation by connecting the
X1 lines.
Standard target
● Square sound-reflective plate used to determine the rated
switching distance sn
● 1 mm thick
● Alignment: vertical to the sonic axis Degree of protection
● Protection of housing against solid bodies and water
● IP65: full protection against dust; protection against of water
● IP67: full protection against dust; protection against submersion
in water at a depth of 1 m for 30 minutes at constant temperature
● IP69K: high pressure cleaning according to DIN 40050-9 based on EN
60529 |